CONCEPT SEALING
From thermoplastics to liquid silicone rubber (LSR).
Certain applications must withstand harmful external influences every single day. For these we develop solutions to seal the corresponding component group reliably and permanently. Our focus lies on the customer’s individual objective.
The Chick Check is an important part of our project planning. This helps us to decide together with our customers which solution fits best – both technically and economically. And in order to finally ensure that the application seals one hundred percent, we also carry out in-house leakage tests during development and serial production in accordance with DIN 40050.
„When sealed also means sealed.“
Learn how Hendrik Book and his colleagues seal components so reliably that they withstand harmful external influences every single day. > Watch now
Four concepts for complete impermeability.
Due to individual requirements and special component geometries, different processes often lead to the same result. Therefore, depending on the requirements, we use different concepts to reliably seal technical plastic parts.
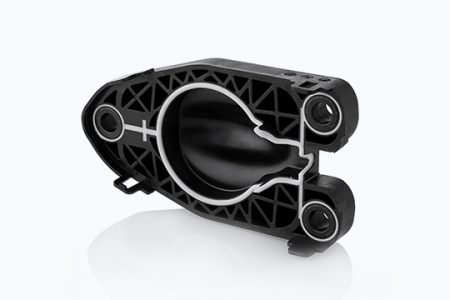
Sophisticated multifunctional parts – gaskets in two-component injection moulding.
By combining different materials, the gaskets are foamed directly onto the component in a single production step. Thus, individual leak tightness requirements are met and complex seal geometries can be produced.
Individual adjustment of seal geometries.
Particularly suitable for complex geometries.
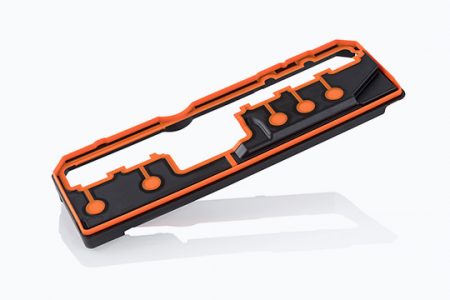
100% tightness at maximum temperatures – with the 2C LSR technology.
For components with very high tightness and temperature requirements, we offer our customers injection molding of two-component liquid silicone rubber (LSR). The 2K LSR technology enables different materials – hard and soft components – to be encapsulated reliably and fully automatically in a single process.
Excellent properties in compression set test.
Good weathering, ageing and UV resistance as well as odour neutrality.
Reliable sealing with high tolerances.
Temperature resistant (from -40°C to +250 °C).
High efficiency for large quantities thanks to a fully automatic, single-stage process.
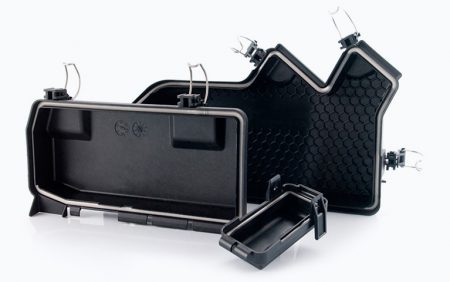
Precise protection for electronic components – with formed-in-place foam gaskets.
Thanks to the FIPFG process, gaskets can be foamed directly into the component irrespective of the tool used and by means of a CNC-controlled system. PUR seals never lose their shape and fit perfectly, even in complex geometries.
Reliable, long-term sealing effect.
Highly accurate fit inside the component.
Seamless joints at the gasket edges.
Tool-independent production of gaskets.
No need to store different types of gaskets.
High productivity (no loss of material due to stamping waste).
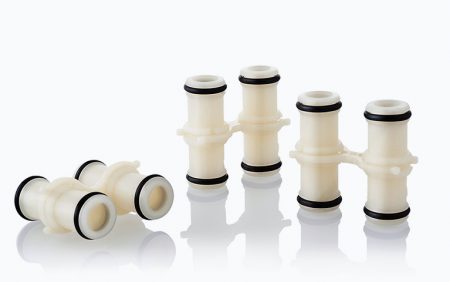
Especially economical – Sealing with moulded parts.
A special solution is not always required, simple standard gaskets can often be used as sealing elements. Different assembly processes promote a safe and economical production.
From flexible processes to a fully automated assembly.
Gaskets can be produced in different materials.
PÖPPELMANN KAPSTO®
Optimal protection for automotive applications.
With our KAPSTO® protection solutions, we offer you optimum protection and maximum process reliability for various automotive applications – from vehicle electrics, engine, fuel management to powertrain and chassis. Discover our range of standards with over 3,000 models available from stock.

CONTACT
Do you have any questions? The K-TECH® team will be happy to answer them.

On-site
Our sales representatives can come straight to your premises. Make an appointment now.

+86 (0) 512 3662 9486
