RAPID TOOLING
Rapid Tooling – Short development times thanks to prototypes and serial production material.
With Rapid Tooling we provide our customer with a way of getting to the finished product in a faster and more economical way. At the same time, we minimise risks and implement item designs or item versions in a more realistic way.
The production of tool inserts using 3D printing reduces risks and costs.
Be it in mechanical engineering, the automotive industry, hydraulics or the sanitary/heating/air conditioning area: users must be able to ensure that tested items work when they are in used in series production. A prototype in the actual material therefore has considerable advantages during development. This is produced using Rapid Tooling at Pöppelmann KAPSTO®. With this regenerative process, the tool insert is manufactured using 3D printing and inserted into an existing master tool mould. Manufacturing from series production material then takes place – e.g. EVA, if the item is to be flexible and soft. In this way, our customers receive almost the identical item that they would get from a steel tool for series production from the printed tool insert for prototyping.
Thanks to Rapid Tooling, customers of Pöppelmann KAPSTO® can get an exact impression of the appearance and characteristics of the future series-produced products during the development phase. Under optimum conditions, near-series production is even possible after just one week. In this way, improvements in the form of modified items can flow directly into current series production on projects in which process or quality problems occur during series production.
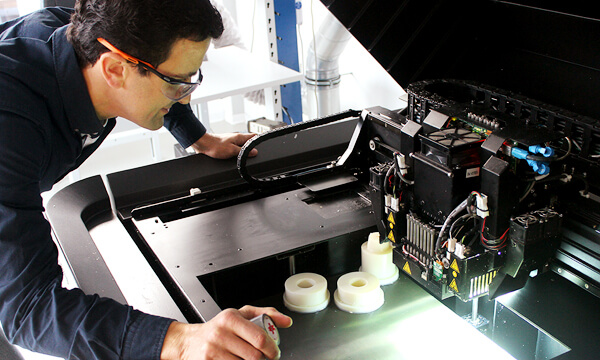
With Rapid Tooling it is not the component itself but the tool for making it that is printed. Depending on the geometry of the item and the material that is used, a few dozen to several hundred layers may be required.
The advantages of Rapid Tooling at a glance:
Ideas become tangible quickly and cost effectively using Rapid Tooling.
With Rapid Tooling it is not the complete item but the tool insert that is produced using 3D printing. However, the master mould is not made from steel. Instead, it is printed in a plastic carrier material, screwed to the master tool mould and fitted to the plastic-processing machine like a normal steel tool. Then the item is manufactured in the actual material. This results in a fully functional component within an extremely short time that can be manufactured more cost effectively since less material is required, for example, and the existing cooling is used.
Of course, a printed tool insert wears more quickly than a steel tool insert, but depending on the geometry of the item, and the material that is used, a few dozen or several hundred layers can be manufactured in this way. It must also be individually checked which geometry can be produced using the basic tools which are currently available. For bigger quantities during the testing and prototyping phase, Pöppelmann KAPSTO® also uses aluminium tools. These can be manufactured much faster and cheaper than steel tools, but can be sufficient for smaller series of several thousand items.
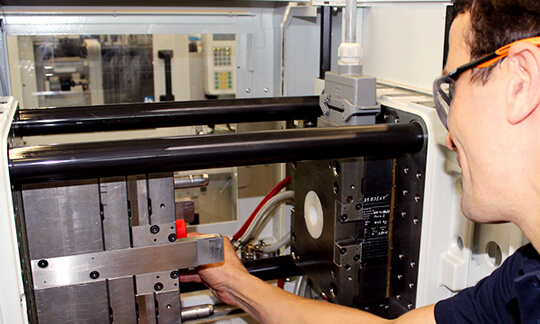
Faster to the finished series-produced product: The printed tool insert is inserted into an existing master tool mould. Then the plastic item is manufactured in the real material.
This could also interest you:
Discover more technology films on our YouKu channel, PöppelmannTV.
CONTACT
Do you have any questions? KAPSTO® team will be happy to answer them.

On-site
Our sales representatives can come straight to your premises. Make an appointment now.

+86 (0) 512 3662 9486
