NEW MOULDS
Success by design: individually produced new moulds.
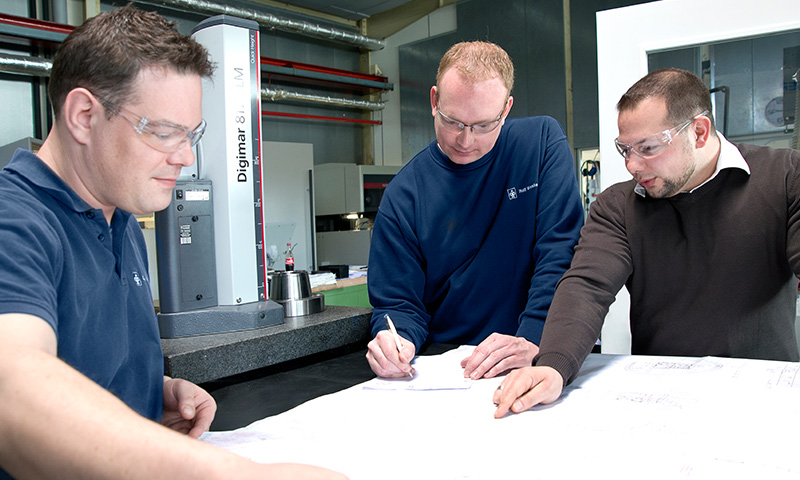
Diverse tasks: our experienced development team during the construction phase.
For over 50 years, we are producing highly specialised new moulds for our customers . These include injection moulds as well as thermoforming moulds. Our injection moulds range from standardised contour inserts all the way to stack moulds. Our thermoforming moulds include pallet moulds along with in-line moulds for articles such as plant pots and plant containers. Each new mould presents us with a new challenge.
Step by step to the target: the process chain.
All our moulds are produced along an innovative process chain – using tried and tested workflows. In this case, the respective sub-processes are checked in the form of “milestones”. By taking this transparent approach, we are able to offer our customers high-quality products with maximum delivery reliability. Let us take a look at each individual step:
New mould enquiry
As part of your enquiry, we clarify the objectives and requirements – including the time schedule.
Quote preparation
Based on your enquiry, we create an individual quote for you, which is of course non-binding.
Order receipt and capacity reservation
Once you decide to proceed with an order, we work with you to define all objectives in the form of a specification document. A detailed time schedule is now also drawn up.
Conclusion and rough planning
The release of the specification documents represents the first ‘milestone’. All previous steps are checked once again. This lays the foundation for the project’s success.
Mould engineering
Once the order is approved, the process of developing and engineering the mould can commence. This also takes place in close contact with the client. The subsequent release of construction data represents the second ‘milestone’.
Detailed and workshop planning
Production of the mould starts with the detailed planning process. Our designers use the Ciamtron CAD-System – and their many years of experience to do this.
Programming
In this step, our team takes all data from engineering and prepares it for mechanical production.
Preparation
Between preprocessing and final processing, the components pass through a quality gate. Here, the dimensional accuracy of the components is carefully checked against check lists. The third ‘milestone’ is now reached.
Final processing
For perfectly formed moulds down to the finest detail: final processing gives the moulds the high precision for our customers’ particular requirements.
Assembly
Following an inspection of steel dimensions, the components are assembled – and the mould is then approved for production. The success of the project is checked once more and the final ‘milestone’ is reached.
INJECTION MOULDS
The right process for every mould.
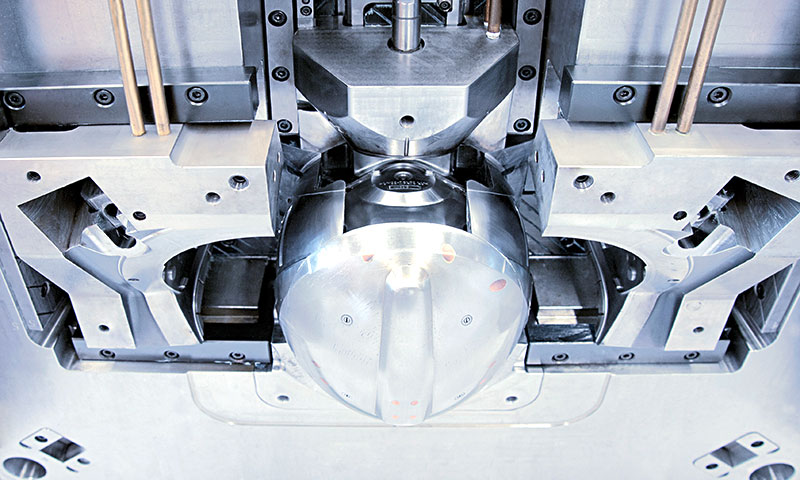
Maximum performance for a customer of the Pöppelmann K-TECH® business division: an injection mould with seven hydraulic and three mechanical slides.
We have already proven our versatility with complex injection moulds for many decades. These are constructed and produced by Pöppelmann WTZ for all four business divisions of our company. In addition to standard moulds, split moulds, and unscrewing moulds, we also produce stacking moulds and multi-injection moulds. Naturally, all moulds are fitted with a hot runner. Thanks to our experience, we can guarantee optimum quality for each order.
Three processes – one goal: perfect moulds.
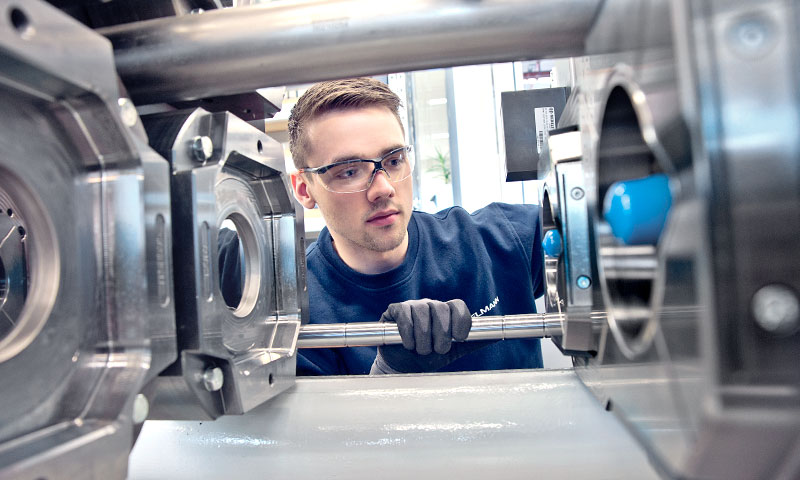
1. Stack technology.
We manufacture stack moulds with up to 48+48 cavities and total weights of up to 8 tons. We use stack technology particularly in the area of thin-walled articles with extremely short production cycles. The use of a second parting plate almost doubles productivity from the same level of machinery usage. The hot runner system is coordinated together with our development partners.

2. The master moulds.
Our master mould concepts offer all customers the option of manufacturing different articles from a single mould. The idea? We create a shared master mould for as many similar products as possible in order to increase productivity. This means that only the contoured components need to be individually produced. By the way, we now even produce master moulds for multi-injection articles!
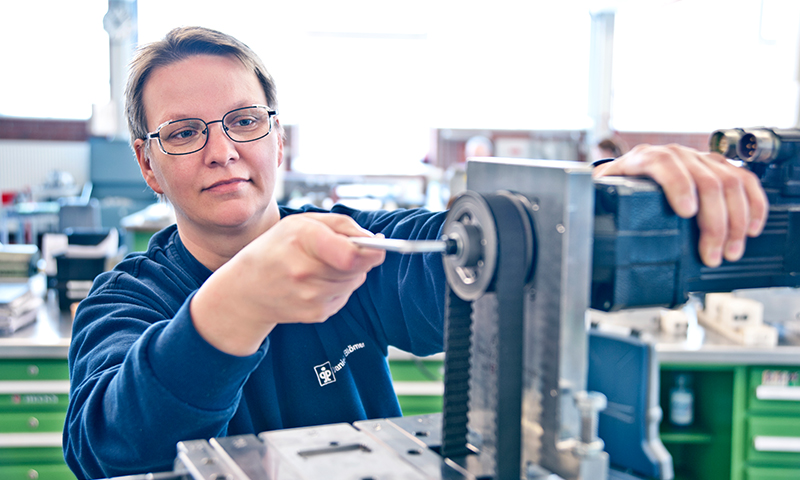
3. Cleanroom production
Moulds for cleanroom production are manufactured in a specially isolated area of Pöppelmann WTZ. Here, we meet the highly specialised requirements of our customers from the medical, pharmaceutical, and food industries.
THERMOFORMING
Innovative mould technology – for fully automated processes.
Pöppelmann WTZ has also been a highly professional and reliable partner to the packaging industry for many years. For the production of thin-walled articles, we produce perfectly matching thermoforming moulds. Here, our focus is on the production of containers for the food industry as well as plant pots and plant pallets for the horticulture sector.
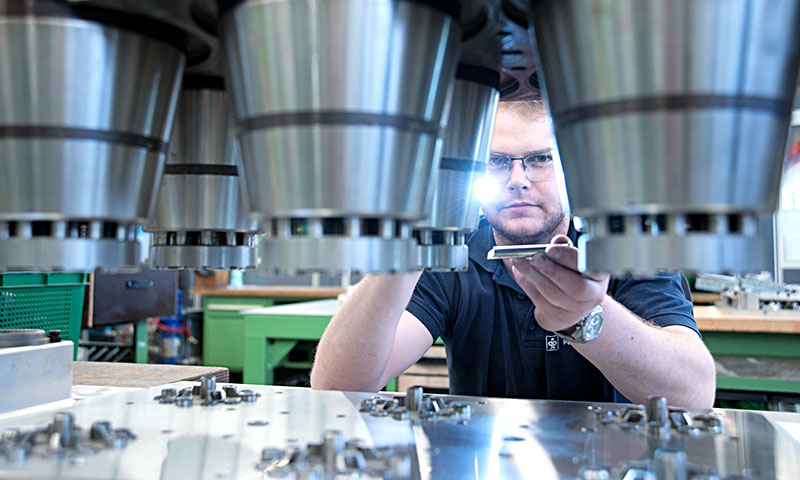
One of many innovative solutions: our patented hole-punching process.
Cost-effective solutions: integration into the process.
Our moulds can be fully integrated into the automated thermoforming process – naturally including the latest-generation machines. In addition to the construction of tray moulds, which requires precise centring in the separate stamp with cycle speeds of up to 32 cycles per minute, we also produce in-line moulds. These are cut immediately after the article is moulded in the same station. This allows our moulds to produce the tightest die clearance tolerances on the article. The benefit to our customers of this approach is obvious: greater efficiency.