TECHNICAL CLEANLINESS
Cleanroom production – technical cleanliness for sensible systems.
Whether fuel injection systems or automotive security systems: plastic parts, whereby even the slightest particle of contamination could lead to their failure, are manufactured by Pöppelmann under increased cleanliness requirements. This is done by specially trained employees in a specifically prepared cleanroom using perfectly matched logistics.
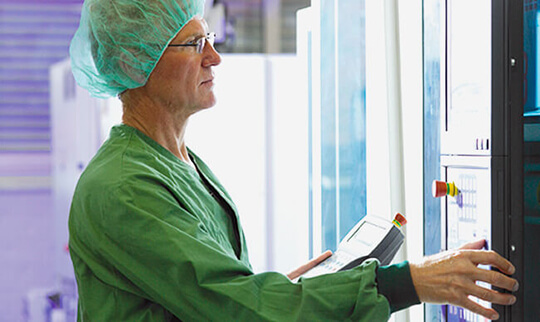
The specially trained Pöppelmann KAPSTO® personnel monitors the entire clean-room production process.
Special air filter systems in the clean-room ensure that purity requirements are met.
Given the ever-increasing miniaturisation, microscopic particles, which are ubiquitous under normal production conditions, can trigger serious malfunctions. By manufacturing in a cleanroom and applying specially matched logistics, Pöppelmann reduces the number and size of such particles to tight limits.
This quality characteristic of injection moulded parts is becoming increasingly important in many industries and it is ensured by regular sampling and documented particle analyses pursuant to volume 19 of the VDA (Association of the German Automotive Industry) and ISO 16232. The air-conditioned cleanroom is spatially separated from the rest of the production and is subject to a continuous positive pressure. The supply air is sucked in through special filters and then moistened.
The injection moulding machines are supplied with pure type raw material via central low-pressure material suction equipment with dust removal function. Robots take the protective elements directly from the injection mould and deposit them in collecting containers that are lined with foil pouches. All these measures work together to guarantee that agreed limits are adhered to or even exceeded.
The advantages of cleanroom production at a glance:
The KAPSTO® clean room
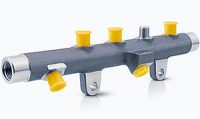
The protection element made by the KAPSTO® business division protect inner and outer contours from mechanical damage and reliably prevent the penetration of dirt into sensitive, safety-relevant and function-critical components.
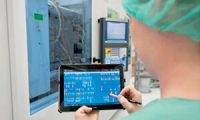
Production takes place in three-shift operation in the clean room at Pöppelmann KAPSTO®. The machinery and tools are optimised for use in the clean room with regard to their design and materials. Specially trained and dressed personnel monitor the entire manufacturing process.
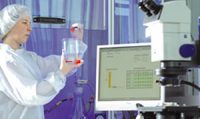
The gravimetric analysis under clean room conditions confirms it: the particle pollution of the finished parts is less than 1 mg per 1,000 cm² of component surface. The automatic typing using the stereo microscope confirms adherence to specifications with regard to the maximum particle size (reflecting) of less than 150 microns, granule (non-reflecting) less than 300 microns and isolated fibres of less than 2,000 microns.
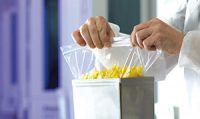
The desired number of protection elements is packed in foil pouches with zip closure, which are then combined into larger units in foil envelopes and forwarded to the despatch department. The packaging prevents any further contamination until use.
This could also interest you:
Discover more technology films on our YouKu channel, PöppelmannTV.
CONTACT
Do you have any questions? KAPSTO® team will be happy to answer them.

On-site
Our sales representatives can come straight to your premises. Make an appointment now.

+86 (0) 512 3662 9486
